HSE: SAFETY MANAGEMENT, POLICIES AND PROCEDURES
Our management team and well-site personnel average over 20 years in the industry and most of their experience is in the fishing sector of the oil and gas industry. The majority of our team has worked together for several years. This elite team is a cohesive unit that shares the same goals and objectives.
It is understood that providing such “high quality service” is in great demand for the drill-ing, completing, recompleting and the plugging and abandoning of oil and gas wells. The goal is to create a solution using a quality product and service that will help our clients reduce their overall cost and reduce the time and risk associated with oil and gas operations. These unique features will place WFR ahead of the competition.
Our employees work hard to create our safety culture and continually strive to establish and maintain a safe work environment for ourselves and our fellow co-workers. Some of the key safety practices we embrace are listed below:
- Stop Work Program
- All employees are active and enthusiastic subscribers of our stop work policy. WFR employees have no reservations to stop work on the count of a safer work environment. Our employees take pride in sharing safe practices with each other and in sending each other home safe each and every day. This is evident by our monthly participation in our stop work cards submitted on a monthly basis. At no time will any employee be reprimanded for stopping work that they believe to be dangerous or a situation that could possibly lead to injury. Everyone has the right to use STOP WORK.
- Behavior Based Safety – S.T.O.P. Cards
- WFR encourages employees to help facilitate a safe working environment by becoming involved in work observations throughout the work areas, both at WFR facilities and on client job sites. S.T.O.P. cards are submitted, reviewed periodically and data trends are evaluated for improvement opportunities to help prevent accidents and injuries. We encourage the use of both our own BBS system as well as client systems at the job site.
- Journey Management Program
- WFR has implemented a journey management plan so that employees become aware of the risk of travel. Employees have been trained to identify and reduce travel related risk via the execution of a journey management plan.
- Training Matrix
- A training matrix is kept by the HSE manager in order to maintain current standing with our employees’ qualifications and training certifications.
- SEMS Program
- Our SEMS program promotes safety and environmental protection during company involved offshore oil & gas operations. The system was developed to identify, address and assist in managing all safety and environmental hazards related to Well Intervention operations. By using API RP 75 as a guidance tool, WFR has established a “Safety and Environmental Management System” with specific objectives geared towards controlling safety hazards and environmental impacts through Employee Training, Operating Procedures, Internal Audits and Reviews.
- ISNetworld® and PEC Subscriber
- WFR is a subscriber to both ISNetworld® and PEC Safety and maintains an updated profile with each of its clients.
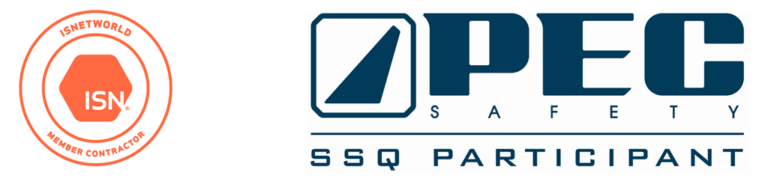